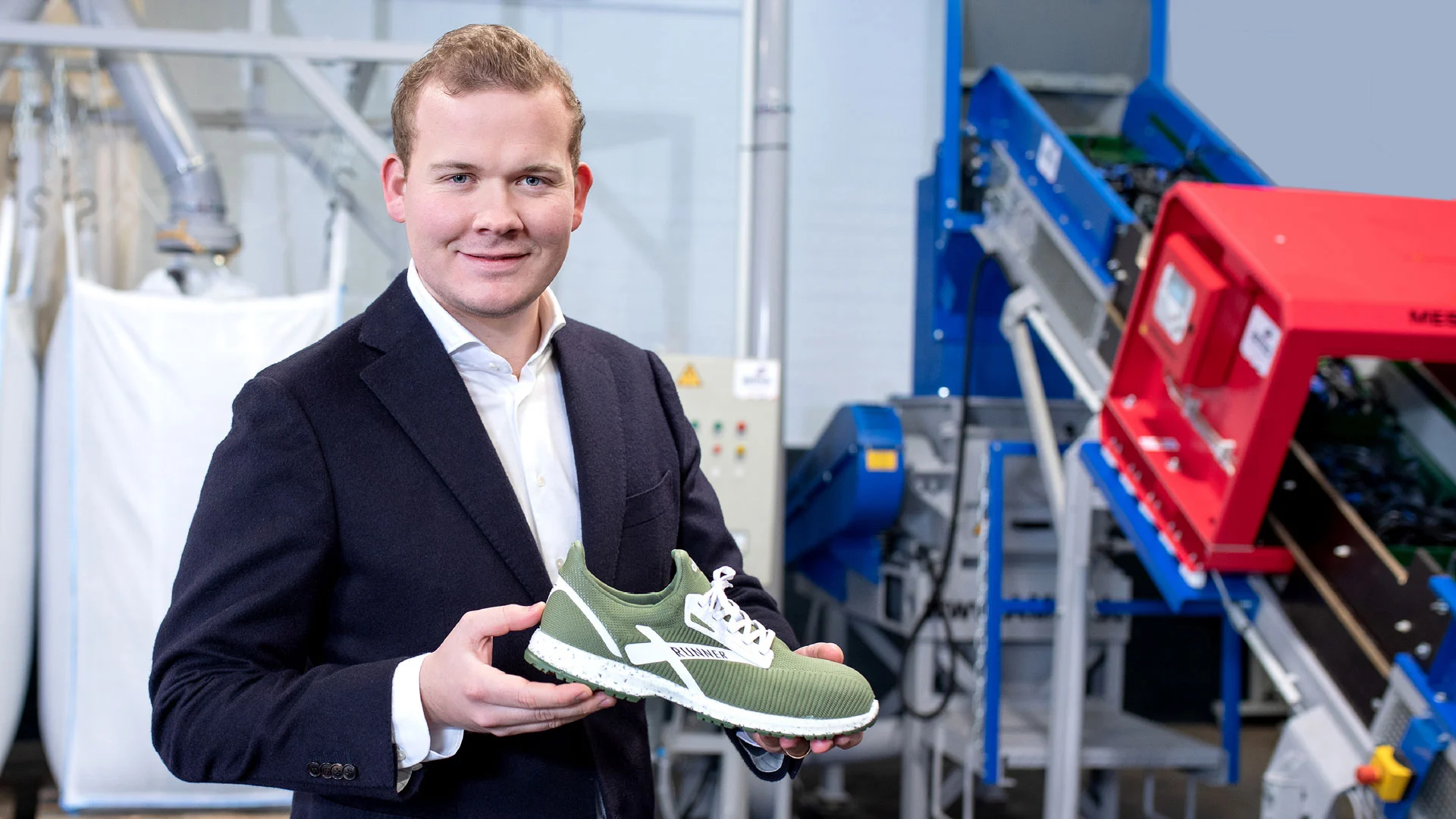
I over 115 år har vi fremstillet robuste og holdbare sikkerhedssko på et af verdens mest moderne skoproduktionsanlæg. Men vi er meget mere end bare en skoproducent. Vi tænker ud over sko. Vores produkter står ikke kun for beskyttelse og sikkerhed, men også for sundhed og en bevidst brug af vores planets ressourcer.
Hendrik Schabsky | CEO ATLAS

FIRE STÆRKE SØJLER
GRUNDlaGET FOR VORES STRATEGI
Vi anvender en bæredygtighedsstrategi baseret på fire søjler.
Vi er forpligtet til løbende at forbedre vores energieffektivitet og reducere vores CO2-udledning for at leve op til vores virksomhedsansvar over for miljøet som en del af vores CSR-initiativer.
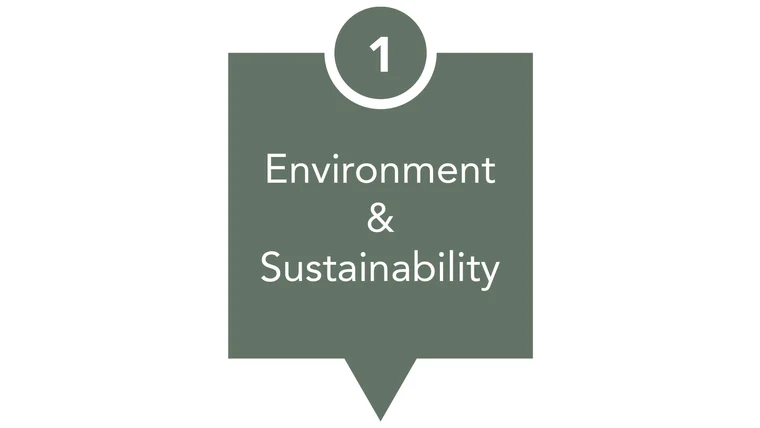
Som en del af vores CSR-strategi er det vores mål at få en betydelig del af de råmaterialer, vi bruger i vores skoproduktion, fra vedvarende kilder. Det skal være med til at reducere vores afhængighed af ikke-vedvarende ressourcer og fremme brugen af bæredygtige materialer.
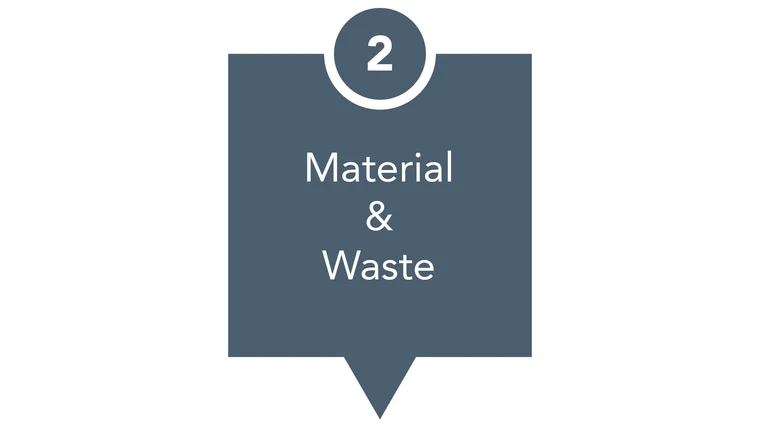
Vores medarbejdere er kernen i vores virksomhed. Sammen brænder vi for det sociale ansvar for at yde et positivt bidrag til samfundet og miljøet.
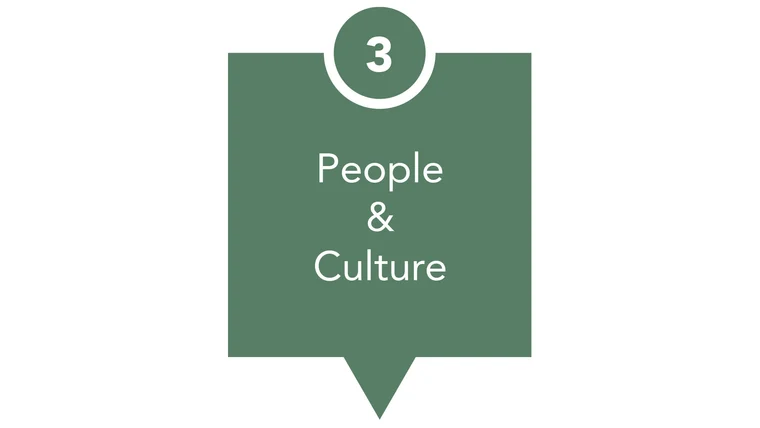
Ved at fremstille vores sikkerhedssko på vores produktionsanlæg i Brasilien og Tyskland har vi en stor del af vores forsyningskæde i vores egne hænder. Vi har langvarige forretningsforbindelser med vores leverandører i Brasilien og Europa, hvilket også skaber gennemsigtighed og tillid.
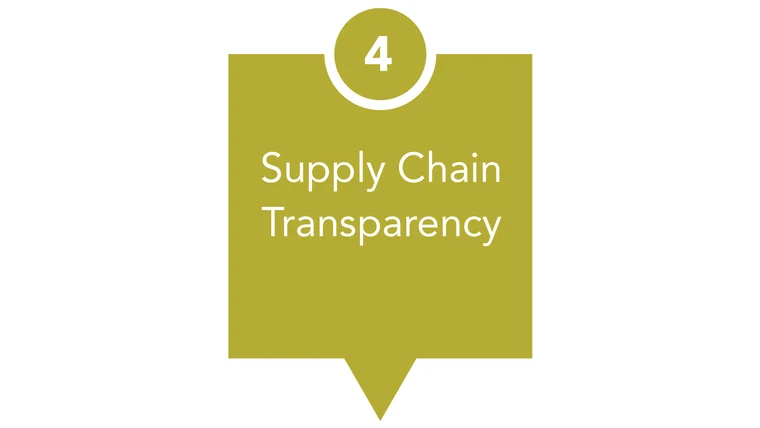