Inauguration de la neuvième machine PU sur le site de Dortmund
Please note: Once you watch the video, data will be transmitted to Youtube/Google. For more information, see Google Privacy.
EXTENSION DES CAPACITÉS DE PRODUCTION
Qualité, innovation, flexibilité et fiabilité sont les éléments les plus importants dans notre collaboration quotidienne. Après la mise en service des septième et huitième machines PU dans les années 2018 et 2019, l'anniversaire de fondation de l'entreprise ATLAS va maintenant être couronné d'un neuvième dispositif d'injection directe PU. La marque ATLAS a ainsi réalisé une nouvelle étape importante pour l'extension des capacités de production sur le site de Dortmund. Trois employé(e)s travaillent aussi dans cette installation en collaboration avec au total 8 robots par équipe et garantissent ainsi une précision et une qualité de réalisation optimales.
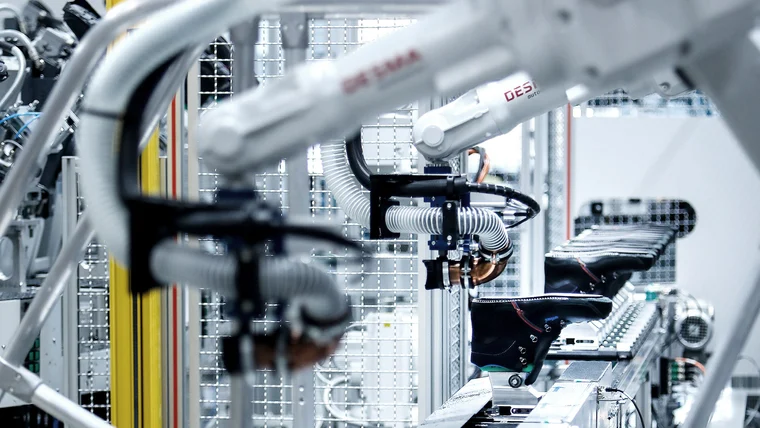

ATLAS ET DESMA
Nous recevons nos machines PU du constructeur d'installations de premier plan à l'échelle mondiale de l'entreprise DESMA à Achim, près de Brême. Après la finition dans l'usine de DESMA, l'installation y est entièrement montée et testée. Ensuite, l'installation est à nouveau démontée et les éléments individuels sont acheminés vers Dortmund dans plusieurs camions surbaissés. Le noyau du carrousel, comme est appelé familièrement le plateau tournant, est le noyau du plateau circulaire de 4 mètres de largeur. C'est sur ce plateau que sont montés les 30 stations d'injection au total une fois que le plateau circulaire a été exactement positionné dans la halle.
TRAVAIL MILLIMÉTRÉ DE PERFECTION
Le montage des éléments de l'installation est un véritable travail d'équipe. Les techniciens expérimentés de ATLAS réalisent ce travail en collaboration avec les spécialistes de DESMA. Toutes les pièces doivent être montées et câblées minutieusement afin que l'installation tourne ultérieurement d'une manière entièrement automatique comme un mouvement d'horlogerie. La première machine PU a été mise en service en 1979 sur le site de Dortmund ; à l'époque, la technique était naturellement bien plus rudimentaire que de nos jours. Beaucoup d'étapes de production devaient alors être réalisées avec beaucoup d'efforts et de sueur, et les semelles aussi étaient soumises à une procédure d'injection avec seulement un produit, le soi-disant PU MONO. Aujourd'hui, nous traitons nos semelles extérieures MPU à deux couches exclusivement avec des matières premières haute technologie.
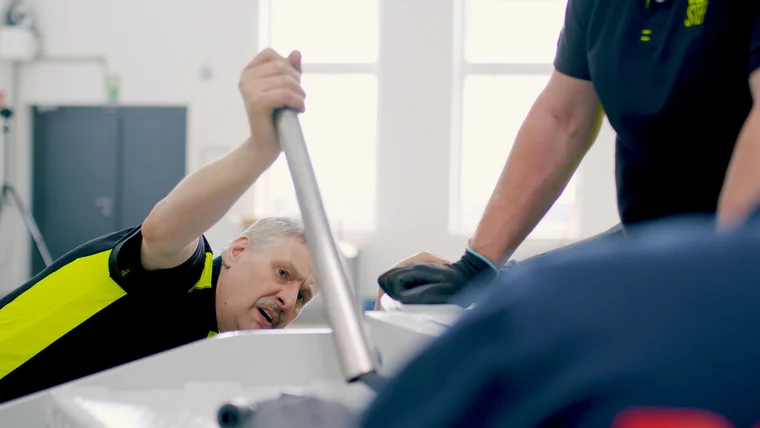
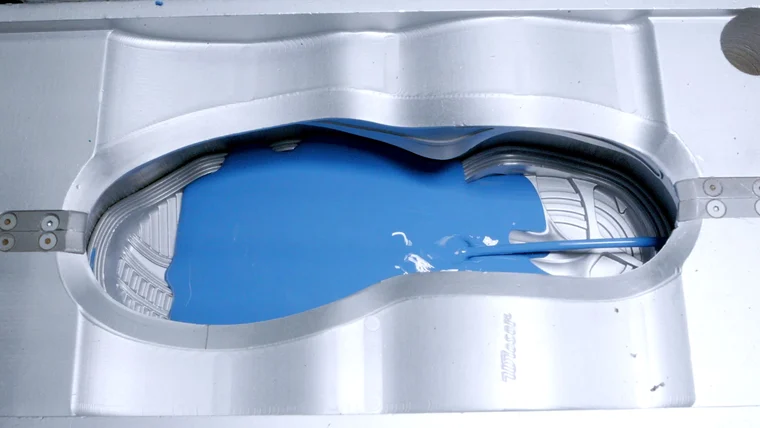
LE MEILLEUR DE DEUX MONDES
MPU signifie polyuréthane multifonctionnel. Nous utilisons ce matériau réalisé selon notre propre formule pour les 2,6 millions de paires de semelles extérieures produites chaque année. Les matières premières nécessitées, le polyol et l'isocyanate, nous sont livrées plusieurs fois par semaine et entreposées dans notre parc à réservoirs de stockage d'une capacité d'environ 50 tonnes. Les deux matières premières sont ensuite affinées par l'ajout d'additifs très différents adaptés au domaine d'application des semelles. Cette procédure s'appelle en jargon : réticulation. Les matières premières sont donc réticulées individuellement et sont ensuite pompées dans la machine de production respective.